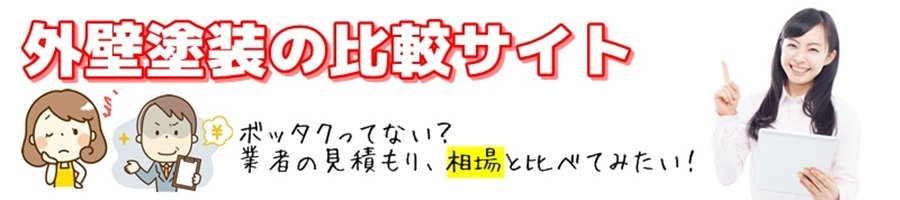
ポリアセタール(POM)は、エンジニアリングプラスチックの中でも特に優れた特性を持つ素材として、様々な産業分野で広く活用されています。正式名称はポリオキシメチレン(Polyoxymethylene)で、POMはその略称です。東日本ではポリアセタール、西日本ではジュラコンと呼ばれることが多いようです。
この素材は、優れた機械的特性と低い吸水性が特徴の高性能プラスチックとして知られています。特に自動車部品や精密機器、電子機器の部品など、高い耐久性と安定性が求められる用途に適しています。
ポリアセタール(POM)の耐熱性は、その用途を決定する上で非常に重要な特性です。POMの耐熱温度は、タイプによって異なります。
ホモポリマータイプの連続使用温度は約85℃、コポリマータイプでは約105℃とされています。短時間であれば、約150℃の高温にも耐えることができます。融点は約165℃、軟化点は約150℃、熱変形温度は約155℃となっています。
荷重たわみ温度(熱変形温度)も1.8MPaで110~120℃程度と比較的高く、高温環境でも本来の強度レベルを維持することができます。そのため、POMはエンジンまわりの部品やヒーターファンなどの材料として適しています。
ただし、長時間の高温環境には適していないという点には注意が必要です。90℃~100℃程度の温度環境であれば連続使用が可能ですが、それ以上の温度では徐々に物性が低下していく可能性があります。
ポリアセタール(POM)は、バランスの取れた機械的強度を持つことが大きな特徴です。具体的な数値で見ると、引張強度は約61MPa、アイゾット衝撃値(ノッチ付き)は約74J/mとなっています。
特に優れているのが耐摩耗性です。POMは自己潤滑性を持つため、他の部品と接触して摺動する部品に最適です。歯車やプーリー、ベアリング用レールなど、機械部品として広く使用されています。
また、金属との摩擦係数が特に低いという特性があります。そのため、アルミやステンレスといった金属との組み合わせにも適しています。実際に、アルミ同士の組み合わせではアルミがすぐに削れて偏芯してしまうような場合でも、アルミとPOMの組み合わせに変更することで寿命が大幅に延びたという事例も多く報告されています。
耐衝撃性にも優れており、外部からの衝撃(瞬間的な大きな力)に対する耐性が高いため、他の部品とぶつかったり床に落ちたりしても簡単には壊れません。これにより、丈夫で信頼性の高い部品を製造することができます。
ポリアセタール(POM)の化学的特性として、耐溶剤性に優れているという点が挙げられます。特に油脂や有機溶剤に対して高い耐性を示すため、様々な環境下での使用に適しています。
吸水性については、わずか0.22~0.25%と非常に低い値を示しています。この低い吸水性により、湿度の影響を受けにくく、寸法安定性に優れているという特徴があります。温度湿度の変化や液体が掛かる部分でも安定した寸法を維持できるため、精密部品の材料として適しています。
ただし、酸やアルカリには弱いという弱点があります。強酸や強アルカリの環境では使用を避けるべきでしょう。また、耐候性もあまり良くないため、屋外での使用は避けた方が良いとされています。
ポリアセタール(POM)は、加工性の良さも大きな特徴の一つです。特に切削加工においては、粘りがなくサクサクと削れるため、CNCマシニングセンタなどでの加工がしやすい素材です。寸法精度も確保しやすく、ソリも発生しにくいため、精密部品の製造に適しています。
製造方法としては、主に以下の2つが一般的です:
ただし、接着性が悪いという特性があるため、一般的に接着による組み立ては困難です。部品の設計段階で、接着に頼らない組み立て方法を考慮する必要があります。
ポリアセタール(POM)の耐熱性をさらに向上させるための技術開発が進んでいます。従来のPOMの耐熱温度は、ホモポリマーで約85℃、コポリマーで約105℃程度でしたが、最新の技術では、これを上回る耐熱性を持つグレードも開発されています。
耐熱性向上のための主なアプローチとしては、以下のようなものがあります:
最新の研究では、ナノコンポジット技術を活用したPOMも開発されています。ナノサイズの無機フィラーを均一に分散させることで、耐熱性だけでなく、機械的特性や寸法安定性も向上させることが可能になっています。
また、環境負荷低減の観点から、バイオベースのPOMの開発も進んでいます。再生可能な植物由来の原料を一部使用することで、石油依存度を下げつつ、従来のPOMと同等の性能を持つ素材の開発が進められています。
これらの技術開発により、POMの適用範囲はさらに広がることが期待されています。特に、より高温環境での使用や、より厳しい条件下での長期使用が可能になることで、新たな用途開発も進んでいくでしょう。
ポリアセタール(POM)は、エンジニアリングプラスチックの一種ですが、他の耐熱樹脂と比較するとどのような位置づけになるのでしょうか。ここでは、POMと他の代表的な耐熱樹脂を比較してみましょう。
まず、耐熱温度の観点から見ると、POMの連続使用温度は約85℃~105℃程度で、一般的なプラスチックよりは高いものの、スーパーエンジニアリングプラスチックと呼ばれる高性能樹脂と比べるとやや低い値となっています。
以下に、代表的な耐熱樹脂との比較を表にまとめました:
樹脂名 | 連続使用温度 | 特徴 | 主な用途 |
---|---|---|---|
POM(ポリアセタール) | 85℃~105℃ | 耐摩耗性、自己潤滑性に優れる | 歯車、ギア、機械部品 |
PC(ポリカーボネート) | 約120℃ | 透明性、耐衝撃性に優れる | 光学部品、電気部品 |
PPS(ポリフェニレンサルファイド) | 200℃~240℃ | 耐熱性、耐薬品性に優れる | 自動車部品、電子部品 |
PEEK(ポリエーテルエーテルケトン) | 約260℃ | 高い耐熱性、機械的強度を持つ | 航空宇宙部品、医療機器 |
PI(ポリイミド) | 260℃~300℃ | 極めて高い耐熱性を持つ | 電子部品、航空宇宙部品 |
ポリアセタール(POM)は、その優れた特性から様々な産業分野で幅広く活用されています。ここでは、POMの具体的な用途事例をいくつか紹介します。
まず、機械部品としての用途が最も一般的です。特に、歯車やギア、ベアリング、カム、レバーなどの摺動部品に多く使用されています。POMの自己潤滑性と耐摩耗性は、これらの部品に最適な特性です。例えば、プリンターやコピー機内部の歯車やローラー部品にもPOMが使用されています。
自動車部品としても広く使用されています。燃料系統の部品、ドアロック機構、ウインドウレギュレーター(窓の開閉機構)、ワイパー機構などに使用されています。特に、エンジンルーム内の部品には、POMの耐熱性と耐油性が活かされています。
電子機器の分野では、スイッチ類、コネクター、ファスナー(留め具)などに使用されています。電気絶縁性と寸法安定性が重要視される部品に適しています。
意外な用途としては、楽器の分野があります。リコーダーや木管楽器、金管楽器の一部にもPOMが使用されています。音響特性と加工性の良さが評価されているようです。
医療機器の分野でも、POMは活用されています。注射器の部品や医療用ポンプの部品など、清潔さと耐久性が求められる部品に使用されています。
日用品の分野では、ファスナー(ジッパー)の歯や時計のバンド、メガネのフレームなどにも使用されています。耐久性と美観を兼ね備えた素材として評価されています。
これらの用途事例からも分かるように、POMは多岐にわたる産業分野で活用されている汎用性の高い素材です。特に、機械的強度と耐摩耗性、寸法安定性が求められる部品に適しています。
ポリアセタール(POM)の耐熱性を最大限に活かすためには、設計段階での配慮が重要です。ここでは、POMの耐熱性を考慮した設計のポイントをいくつか紹介します。
まず、使用環境の温度条件を正確に把握することが重要です。POMの連続使用温度は、ホモポリマーで約85℃、コポリマーで約105℃程度ですが、短時間であれば150℃程度まで耐えることができます。ただし、長時間の高温環境では物性が低下する可能性があるため、使用環境の最高温度と暴露時間を考慮した設計が必要です。
次に、熱膨張を考慮した設計が重要です。POMは、金属に比べて熱膨張係数が大きいため、温度変化による寸法変化を考慮する必要があります。特に、金属部品とPOM部品を組み合わせる場合は、温度変化による寸法差を考慮した設計が必要です。
また、熱がこもりやすい構造は避けるべきです。POMは熱伝導率が低いため、熱がこもりやすい構造では局所的な温度上昇が起こる可能性があります。放熱を考慮した設計や、必要に応じて放熱フィンなどを設けることも検討すべきでしょう。
さらに、応力集中を避ける設計も重要です。POMは、高温環境下では機械的強度が低下するため、応力集中が起こりやすい急激な断面変化や鋭角的な形状は避けるべきです。適切なフィレット(角の丸め)やリブ構造を設けることで、応力分散を図ることができます。
耐熱グレードの選定も重要なポイントです。POMには様々なグレードがあり、耐熱性を強化したグレードも存在します。使用環境に応じて適切なグレードを選定することで、より高い信頼性を確保することができます。
最後に、試作評価の重要性を忘れてはなりません。設計段階での計算や予測だけでなく、実際の使用環境を模擬した条件での試作評価を行うことで、予期せぬ問題を事前に発見し、対策を講じることができます。
これらのポイントを考慮すること