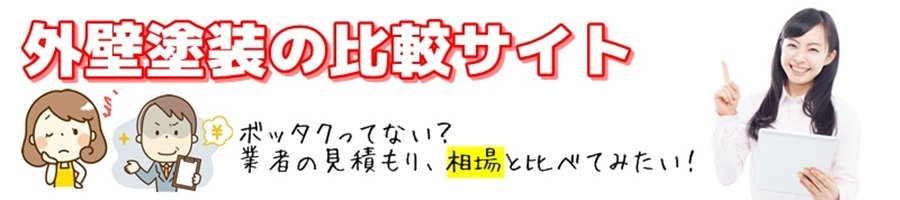
冷間加工(冷間鍛造)とは、金属材料を常温(室温)の状態で圧力を加えながら成形する加工技術です。この技術は建築部材や構造部品の製造において重要な役割を果たしています。
冷間鍛造と他の鍛造方法の主な違いは加工温度にあります。以下にその特徴を比較してみましょう。
冷間鍛造では材料を加熱しないため、熱膨張や冷却による寸法変化がほとんど発生しません。これにより、非常に高い寸法精度を実現できます。建築金具や接合部品など、正確な寸法が要求される部品の製造に適しています。
また、冷間加工では金属の結晶構造が細かくなり、より均一な材料特性が得られます。これにより表面が滑らかになり、高品質な表面仕上げが可能になります。建築用金具の美観や耐食性向上にも貢献しています。
建築施工において、材料コストは全体コストの大きな部分を占めています。冷間加工の最大のメリットの一つは、材料の利用効率が非常に高いことです。
切削加工と比較すると、冷間鍛造では材料のスクラップが極めて少なく、歩留まりが良好です。具体的には、切削加工に比べておよそ71%もの材料節約が可能になります。これは建築部材の製造において大きなコスト削減につながります。
例えば、ある製品の場合。
この差は、大量生産時には非常に大きなコスト差となります。建築金具や接合部品などの製造において、この省資源効果は見逃せないメリットです。
また、冷間鍛造では材料を無駄なく使用できるため、環境負荷の低減にも貢献します。建築業界でも環境配慮が求められる現代において、この点は重要な利点と言えるでしょう。
建築部材の製造において、生産効率は非常に重要な要素です。冷間鍛造は生産性の面でも大きなメリットを持っています。
切削加工の加工スピードが分単位であるのに対し、冷間鍛造のスピードは秒単位です。一般的に、一分間に10~50個、おおよそ一個2秒程度での加工が可能です。この生産スピードの差は、大量生産時には非常に大きな差となります。
具体的な例を挙げると。
これを1時間あたりの生産量に換算すると。
この約30倍もの生産性の差は、建築金具や接合部品の製造コストに大きく影響します。特に大量生産が必要な標準部品の製造において、この生産性の向上は大きなコストダウンにつながります。
また、冷間鍛造ではプレス工程のみでネットシェイプ(部品の最終形状)やニアネットシェイプ(2次加工で最終形状となる半製品)の状態まで加工できるため、リードタイム短縮にもつながります。これにより、建築プロジェクトの工期短縮にも貢献できます。
建築部材において耐久性は非常に重要な要素です。冷間加工には、材料の機械的性質を向上させる効果があります。
冷間鍛造では、塑性変形による圧縮応力により、材料の硬度や強度が向上します。これは「加工硬化」と呼ばれる現象で、金属の結晶構造が変化することで強度が増します。
また、冷間鍛造によって形成される「メタルフロー」(内部組織が繊維状に連続してつながった状態)により、部品の強度や耐摩耗性が向上します。これは建築金具や構造部材の耐久性向上に大きく貢献します。
具体的なメリット
これらの特性向上により、建築部材の長寿命化やメンテナンスコスト削減にもつながります。特に、繰り返し荷重がかかる接合部や、摩擦が生じる可動部などの部品製造において、冷間鍛造の特性は大きなメリットとなります。
冷間加工技術は従来、工場での部品製造が中心でしたが、近年では建築施工現場での応用も広がりつつあります。特に、現場での金属加工や接合部の成形などに冷間加工の原理が応用されています。
建築施工現場での冷間加工技術の応用例
これらの応用により、建築施工の品質向上やコスト削減、工期短縮などが期待できます。
また、最新の研究では、アルミニウム合金やチタン合金など、従来は冷間加工が難しいとされていた材料への応用も進んでいます。これにより、より軽量で高強度な建築部材の製造が可能になりつつあります。
アルミニウム合金の冷間鍛造に関する最新研究
将来的には、デジタル技術と組み合わせた「スマート冷間加工」も期待されています。例えば、センサーと連動した冷間加工機により、材料の状態をリアルタイムで監視しながら最適な加工条件を自動調整するシステムなどが研究されています。これにより、さらなる品質向上や効率化が期待できます。
建築部材の製造において、冷間加工が常に最適というわけではありません。用途や要件に応じて、最適な加工方法を選択することが重要です。ここでは、冷間加工と他の主要な加工方法を比較し、選択基準を解説します。
冷間鍛造と切削加工の比較
評価項目 | 切削加工 | 冷間鍛造 |
---|---|---|
材料歩留まり | △ | ◎ |
加工スピード | △ | ◎ |
製品強度 | ○ | ◎ |
加工精度 | ◎ | ○ |
加工自由度 | ◎ | ○ |
少量生産 | ◎ | △ |
大量生産 | △ | ◎ |
試作納期 | ◎ | △ |
量産納期 | ○ | ◎ |
金型 | 不要 | 必要 |
冷間鍛造、温間鍛造、熱間鍛造の比較
特徴 | 熱間鍛造 | 温間鍛造 | 冷間鍛造 |
---|---|---|---|
鍛造温度 | 1100°C~1250°C | 300°C~850°C | 常温(室温) |
鍛造荷重 | 低い | 中 | 高い |
寸法精度 | △ | ○ | ◎ |
表面仕上り | △ | ○ | ◎ |
複雑形状加工 | ◎ | ○ | △ |
生産数量 | 中・小量生産向き | 中量生産向き | 大量生産向き |
最適な加工方法の選択基準としては、以下の点を考慮するとよいでしょう。
建築部材の製造においては、これらの要素を総合的に判断し、最適な加工方法を選択することが重要です。例えば、標準的な接合金具など大量生産が必要な部品には冷間鍛造が適している一方、特殊な形状の一点ものには切削加工が適しているといった具合です。
冷間加工には多くのメリットがある一方で、いくつかのデメリットも存在します。建築部材の製造においてこれらのデメリットを理解し、適切に対処することが重要です。
冷間加工の主なデメリット
デメリットを克服するための技術的アプローチ
これらのデメリットに対して、以下のような技術的アプローチで克服を図ることができます。
冷間鍛造における潤滑技術の最新動向
建築部材の製造においては、これらの技術的アプローチを適切に組み合わせることで、冷間加工のデメリットを最小限に抑えつつ、そのメリットを最大限に活かすことが可能になります。特に、大量生産が見込まれる標準部品については、初期の金型投資を回収できる見込みがあれば、冷間加工の採用が有利になることが多いでしょう。
また、近年ではデジタルツインやAI技術を活用した金型設計・製造プロセスの最適化も進んでおり、従来よりも効率的かつ低コストでの金型製作が可能になりつつあります。これにより、冷間加工の適用範囲がさらに広がることが期待されています。