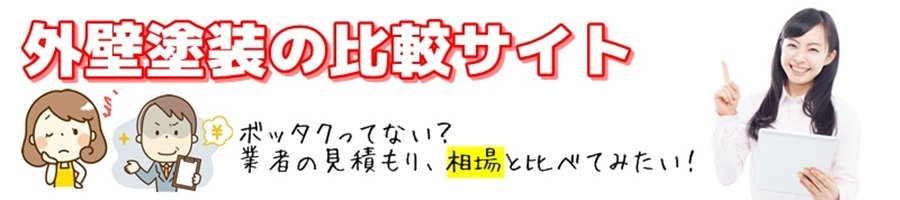
キャップ溶接は配管システムにおいて極めて重要な技術であり、特にTIG溶接(Tungsten Inert Gas溶接)との組み合わせで高品質な仕上がりを実現できます。TIG溶接によるキャップ溶接では、タングステン電極から発生するアークによって母材を溶融し、キャップと配管を一体化させます。
この技術の核心となるのは、溶接部の内部酸化防止です。配管内部に不活性ガス(主にアルゴンガス)を充填することで、溶接時の高温による酸化を防ぎ、耐食性と強度を維持します。特にステンレス鋼やチタン、ニッケル合金などの高級材料では、この酸化防止対策が品質を左右する重要な要素となります。
TIG溶接でキャップ溶接を行う際の重要なポイント。
実際の作業現場では、従来のテープや簡易養生では限界があるため、専用のシリコンキャップが開発されています。このシリコンキャップは高耐熱性を備え、繰り返し使用が可能なため、作業効率とコストパフォーマンスの向上に大きく貢献しています。
レーザー溶接技術は、キャップ溶接の精密性と効率性を飛躍的に向上させる革新的な手法です。特に大量生産や高精度が要求される案件において、その真価を発揮します。
実際の活用事例として、プレートの指定箇所にキャップを溶接する製品があります。この製品では、プレートに開けた孔に他の部品を差し込む際、キャップが塗装時のマスキング機能を果たします。レーザー溶接のスポット径が0.6mmという極めて細い点で溶接を行うため、熱影響部が最小限に抑えられ、周囲への変形や変色を防げます。
レーザー溶接の主な利点。
しかし、レーザー溶接には課題もあります。特に注意すべきは母材の反りや変形です。プレートに矯正しきれない反りがある場合、プログラムした溶接位置とのズレが発生し、最大0.4mm程度のズレでも溶接不可となる場合があります。この問題への対策として、事前の材料検査と治具設計の最適化が不可欠です。
品質安定化のための技術的対応。
キャップ溶接において正確な寸法と品質を確保するためには、JIS規格の理解と適切な継手選定が不可欠です。JIS B2312-2015(配管用鋼製突合せ溶接式管継手)では、キャップの詳細な寸法基準が規定されています。
主要な寸法規定内容。
JIS規格では、キャップの厚さについて「限界厚さ」という概念が導入されています。背から端面までの距離は、厚さが限界厚さ未満の場合はE、限界厚さ以上の場合はE1として区別されます。これにより、使用圧力と安全率に応じた適切な肉厚選定が可能となります。
ステンレス鋼キャップの場合、10S、20S、40Sといったスケジュール番号による分類が一般的です。各スケジュールの特徴は以下の通りです。
10Sスケジュール(薄肉)
20Sスケジュール(標準)
40Sスケジュール(厚肉)
選定時の重要な検討事項。
高品質なキャップ溶接を実現するためには、溶接部の酸化防止が極めて重要です。特にステンレス鋼、チタン、ニッケル合金等のスーパーアロイでは、内部酸化が発生すると溶接部の耐食性と機械的性質が著しく低下します。
バックシールド技術の基本原理は、配管内部に不活性ガスを充填し、溶接時に発生する高温から溶接金属を保護することです。一般的に使用されるガスの種類と特性。
アルゴンガス(Ar)
ヘリウムガス(He)
混合ガス(Ar+H2等)
従来の酸化防止方法では、テープやビニールシートを使用した簡易的な方法が主流でしたが、これらには以下の問題がありました。
これらの課題を解決するため、専用のシリコンキャップが開発されています。シリコンキャップの主な特徴。
実際の施工手順。
キャップ溶接の品質管理において、従来の外観検査や浸透探傷検査に加えて、独自の検査手法を導入することで、より高い品質保証が可能となります。
革新的な検査技術の活用
近年注目されているのが、超音波厚さ測定による溶接部の内部品質評価です。従来の放射線透過試験では発見が困難な微細な内部欠陥も、高周波超音波技術により非破壊で検出できます。特に、以下の欠陥検出に効果を発揮します。
デジタル技術を活用した品質記録システム
品質管理の効率化と信頼性向上のため、デジタル技術を活用した記録システムの導入が有効です。
統計的品質管理の導入
大量生産におけるキャップ溶接では、統計的品質管理(SQC)の手法が効果的です。具体的な管理項目。
作業者技能の標準化
キャップ溶接の品質は、作業者の技能に大きく依存します。技能の標準化と向上のための取り組み。
環境因子の管理
溶接品質に影響を与える環境因子の管理も重要です。
これらの品質管理手法を組み合わせることで、キャップ溶接の信頼性を大幅に向上させることができます。特に、サニタリー配管、食品、医薬、半導体分野では、極めて高い品質レベルが要求されるため、これらの管理手法の導入は不可欠といえるでしょう。
継続的な改善活動を通じて、キャップ溶接技術のさらなる向上を図り、産業界の発展に貢献していくことが重要です。