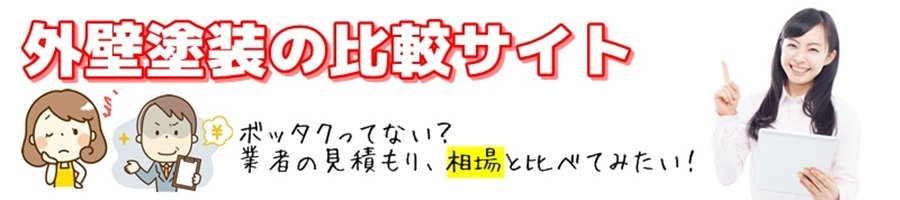
ユニットバスの誕生は、1964年の東京オリンピックにまで遡ります。当時、急増する観光客に対応するため、ホテルニューオータニの建設が計画されました。この17階建て全1058室の大規模ホテルを、わずか17カ月という超短期間で完成させる必要がありました。
通常、1000室を超えるホテル建設には3年以上かかると言われていた時代に、この工期を実現するためには革新的な建築技術が必要でした。特に浴室工事は時間がかかる工程であったため、工期短縮と浴室の軽量化が急務となりました。
設計施工を担当した大成建設からの依頼を受けたTOTOは、浴室のプレハブ化に取り組み、「セミキュービック方式のユニットバス」を開発しました。この方式では、工事中の運搬を容易にするために上下に分けた構造を採用し、器具や給排水管を組み込んだ腰フレームと上部壁フレームを工場でそれぞれ組み立てる方法を取りました。
浴室の軽量化においては、それまで使用されていた陶器に代わり、FRP(繊維強化プラスチック)を浴槽と洗面カウンターに採用。これにより、従来2トンを超えていた浴室の重量を730kg程度まで軽量化することに成功しました。一方で、利用者に違和感を与えないよう、床は日本人が慣れ親しんだタイル張りを維持するという配慮も行われました。
この革新的な工法により、ホテルニューオータニの1044室に対するユニットバスの据え付け工事をわずか2カ月で完了させるという驚異的な成果を上げました。この時に開発された考え方が、現代のユニットバスの原型となり、今日まで引き継がれています。
ユニットバスの工法は、従来の「在来工法」と比較して多くの特徴があります。在来工法は、現場で一から壁や床、防水工事を施工して仕上げる方法で、タイルや天然石など好みの素材を選んで自由にデザインできる利点があります。一方、ユニットバスは工場で製造されたパーツを現場で組み立てる方式のため、規格に沿った設計となります。
ユニットバスの主な特徴は以下の通りです。
一方で、ユニットバスには以下のような制約もあります。
近年では、在来工法とユニットバスの良い点を融合した「ハーフユニットバス」も注目されています。これは、在来工法の自由度とユニットバスの防水性を兼ね備えたハイブリッドな施工方法で、より多様なニーズに応えることができます。
ユニットバスは大きく分けて3種類あり、それぞれ用途や設置場所によって選び分けることが重要です。建築プロジェクトに最適なユニットバスを選ぶためのポイントを解説します。
1. 1点ユニットバス(システムバス)
2. 2点ユニットバス
3. 3点ユニットバス
ユニットバスを選ぶ際の重要なポイントは以下の通りです。
建築プロジェクトにおいては、これらのポイントを総合的に判断し、用途や予算に合ったユニットバスを選定することが成功の鍵となります。
ユニットバスの施工技術は、1964年の誕生から現在に至るまで、大きく進化してきました。TOTOのユニットバス50年史によると、その発展は「創成期(1964年~1985年)」「拡大期(1986年~2000年)」「進化期(2001年~2014年)」の3つの時代に大別されます。
**創成期(1964年~1985年)**では、新しいユニット工法の開発に始まり、マイホーム時代の到来に応じて、新築マンション用、新築戸建て用と住宅用への商品化が進みました。1966年には集合住宅向け標準ユニット「UB-S1」が発売され、床、壁、天井の3つに分割し、幅600mmのパネルを基本モジュールとして部材を標準化する「パネル方式」が採用されました。また、ユニットの内側から組み立てられる「内組構造」も取り入れられました。
1977年には戸建住宅用浴室ユニット「KBシリーズ」が発売されました。これは、夏場に工事が集中する北海道で工期短縮が求められたことがきっかけでした。工場で組み立てまで済ませ、現地に運んで設置工事を行う「キュービック方式」を採用し、保温性を高めるための工夫も施されました。これ以降、全国にユニットバスが普及していくことになりました。
**拡大期(1986年~2000年)**では、ユニットバスの普及率が拡大するにつれて、量産対応体制や多品種、システム化などが求められるようになりました。デザイン性も重視されるようになり、壁パネルの目地(パネルとパネルの間を埋める樹脂素材)がデザインを損なうという課題に対して、「目地なしカール構造」が開発されました。この構造は、20年以上経った今も採用され続けています。
また、高齢者への配慮から浴室のバリアフリー化へのニーズが高まり、1997年にはマンション用の「低床シリーズ」が発売されました。浴室の入り口の段差を85mmから12mmに、浴槽のまたぎの高さを540mmから450mmへと低くし、構造上脱衣所よりも浴室を掘り下げる必要がある場合でもその高さ(沓摺=くつずり)を低くすることを実現しました。この「低床」設計は、その後もマンションのスタンダードとなっていきました。
**進化期(2001年~2014年)**の代表的な技術革新は、「カラリ床」と「魔法びん浴槽」です。FRPの床は防水機能は高いものの水が残り乾きにくいという課題がありました。これを解決するため、夜入浴して翌朝には乾く「カラリ床」が2001年に発売されました。また、お湯が冷めやすいという不満に応えて、魔法びんのような二重断熱構造により、6時間たっても2℃しか冷めない「魔法びん浴槽」が2004年に発売されました。これらの技術は、現在の日本のユニットバスでは標準的な機能となっています。
さらに、カラリ床を進化させ、硬い床から柔らかい踏み心地を求めて、2008年に「ソフトカラリ床」が開発され、2012年には床の素材を断熱性の高い素材に変え、さらに心地よさを向上させたW断熱構造「ほっカラリ床」が開発されるなど、ユニットバスは常に進化を続けています。
現在では、IoT技術を活用したスマートバスや、さらなる省エネ性能の向上、高齢者や障害者にも使いやすいユニバーサルデザインの採用など、ユニットバスの技術革新は続いています。
近年の建築業界では、環境配慮やSDGs(持続可能な開発目標)への取り組みが重要視されており、ユニットバス製造・施工においてもその流れは顕著です。ユニットバスの環境配慮型設計と施工は、建築プロジェクト全体の持続可能性に大きく貢献しています。
省エネルギー設計の進化
現代のユニットバスは、高断熱・高気密設計が標準となっています。壁・床・天井に断熱材を効果的に配置することで、浴室内の温度を保持し、ヒートショックの防止と同時に、暖房エネルギーの削減にも貢献しています。特に「魔法びん浴槽」に代表される断熱浴槽は、湯温の低下を抑制することで追い焚き回数を減らし、エネルギー消費量の削減に寄与しています。
最新の製品では、LED照明の採用や、節水型シャワーヘッドの標準装備など、使用時のエネルギー・水資源消費を抑える工夫が随所に見られます。これらの技術は、SDGsの目標7「エネルギーをみんなに、そしてクリーンに」や目標6「安全な水とトイレを世界中に」に直接貢献しています。
資源循環への取り組み
ユニットバスの製造過程では、リサイクル素材の活用も進んでいます。FRP(繊維強化プラスチック)の一部にリサイクル材を使用したり、解体時の分別を容易にする設計を採用したりすることで、資源の有効活用と廃棄物削減を実現しています。
また、長寿命設計も重要な取り組みの一つです。耐久性の高い素材の採用や、部品交換が容易な設計により、ユニットバス全体の寿命を延ばし、廃棄物の発生を抑制しています。これはSDGsの目標12「つくる責任、つかう責任」に合致する取り組みと言えます。
施工時の環境負荷低減
ユニットバスの施工は、在来工法と比較して工期が短く、使用する材料も少ないため、施工時の環境負荷が低減されます。工場での一括生産により、現場での廃材発生を最小限に抑えられるほか、騒音や粉塵の発生も抑制できます。
さらに、工場生産による品質の安定は、施工不良による手直し工事の減少にもつながり、結果として資源やエネルギーの無駄を削減しています。これらの取り組みは、SDGsの目標11「住み続けられるまちづくりを」や目標9「産業と技術革新の基盤をつくろう」に貢献しています。
健康・快適性への配慮
環境配慮だけでなく、使用者の健康や快適性への配慮も進んでいます。抗菌・防カビ素材の採用や、清掃のしやすさを考慮した設計は、衛生的な浴室環境の維持に役立っています。また、ヒートショック対策としての断熱性能向上は、特に高齢者の健康維持に貢献しています。
これらの取り組みは、SDGsの目標3「すべての人に健康と福祉を」に合致するものであり、建築物の価値向上にもつながっています。
今後の展望
ユニットバス業界では、さらなる環境負荷低減に向けた技術開発が進んでいます。例えば、浴室で使用した水を再利用するグレーウォーターシステムの組み込みや、太陽光発電との連携による自然エネルギー活用など、より高度な環境配慮型設計が模索されています。
建築従事者としては、これらの環境配慮型ユニットバスの特性を理解し、プロジェクトに適切に取り入れることで、建築物全体の環境性能向上に貢献することが求められています。SDGsへの取り組みは、単なる社会的責任を超えて、建築物の付加価値創出にもつながる重要な要素となっています。