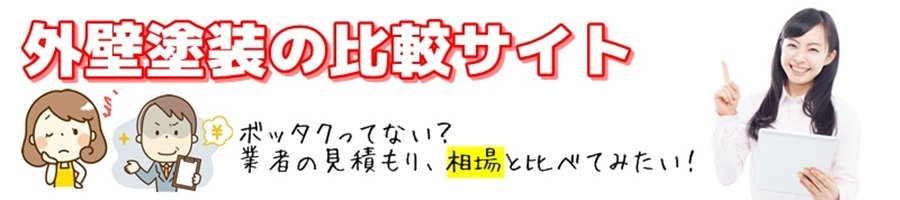
DV継手の寸法表は、JIS K6739「排水用硬質ポリ塩化ビニル管継手」に基づいて規定されています。この規格では、φ30からφ150までの呼び径について、詳細な寸法基準が設けられています。
基本的な寸法項目として以下が定められています。
例えば、呼び径50mmのDV継手の場合、d1は60.35mm(許容差±0.30)、d2は59.75mm(許容差±0.30)、差し込み長さは25mm(許容差±1)となっています。これらの寸法は製造時の品質管理において厳格に管理されており、施工現場での確実な接続を保証しています。
特に注目すべきは、許容差の設定です。呼び径が大きくなるほど許容差も大きく設定されており、例えば150mm継手では外径の許容差が±0.45mmとなっています。この設計により、製造時のばらつきを吸収しながら、確実な接続性能を確保しています。
DV継手寸法表を効果的に活用するためには、各項目の意味と相互関係を正しく理解することが重要です。
寸法表の見方のポイント。
実際の継手選定では、接続する管の外径と継手の内径(d2)の関係が最も重要になります。例えば、VU管50mmの外径は60.0mmですが、DV継手50mmの内径d2は59.75mm(許容差±0.30)となっており、確実な嵌合が可能な設計となっています。
差し込み長さ(ℓ)は施工時の重要な管理項目で、この値が不足すると接続強度が低下し、過剰になると継手内部で応力集中が発生する可能性があります。寸法表では、呼び径30mmで18mm、50mmで25mm、100mmで50mmといったように、管径に応じて適切な差し込み長さが規定されています。
また、継手の肉厚(t1、t2)は耐圧性能に直結する重要な要素です。特に大口径になるほど肉厚も厚く設定されており、150mm継手では最小肉厚が6.3mmと規定されています。
DV継手には多様な種類があり、用途に応じた適切な選定が必要です。寸法表を活用することで、最適な継手を効率的に選定できます。
主要な継手種類と特徴。
特に注目すべきは、90°大曲りエルボの設計です。通常のエルボと比較して曲率半径が大きく設定されており、圧力損失を最小限に抑える設計となっています。寸法表では、呼び径65mmの場合、Z1が33mm、Z2が90mm、Z3が125mmと規定されており、これらの寸法が最適な流体性能を実現しています。
径違い継手の選定では、両端の呼び径の組み合わせが重要になります。例えば、100×75mm径違いY継手では、大径側(100mm)と小径側(75mm)それぞれに対応した寸法が設定されており、Z1が40mm、Z2が110mm、Z3が150mmとなっています。
VU-DV継手は、AS38規格に基づく特殊な継手で、VU管とDV管の接続に使用されます。この継手では、両端で異なる管種に対応するため、それぞれに最適化された寸法設定がなされています。
効率的な施工を実現するためには、事前の詳細な計画立案が不可欠です。DV継手寸法表を活用することで、精度の高い施工計画を作成できます。
施工計画での寸法表活用ポイント。
特に重要なのは、継手の全長寸法(L寸法)を正確に把握することです。例えば、ソケット継手の場合、呼び径50mmでL寸法が53mmとなっており、これを配管設計に反映させることで、正確な管割り付けが可能になります。
複合継手の場合、寸法がより複雑になります。90°大曲りY継手(WLT)では、L1、L2、L3の3方向の寸法が規定されており、呼び径75mmの場合、L1が78mm、L2が140mm、L3が100mmとなっています。これらの寸法を3次元的に考慮した設計により、狭小空間でも効率的な配管が可能になります。
また、差し込み長さの管理も重要です。各継手について規定された差し込み長さを確実に確保することで、設計強度を満足する接続が実現できます。現場での管理では、差し込み深さマーキングを活用することで、目視による確実な施工管理が可能になります。
DV継手の品質管理において、寸法表の正確な理解と適用は極めて重要です。特に大規模な排水設備工事では、継手一つ一つの品質が全体システムの性能を左右します。
品質管理の重要項目。
受入検査では、特に外径(d1)と内径(d2)の寸法確認が重要です。製造時のばらつきが許容差内に収まっているかを確認することで、現場での接続不良を未然に防ぐことができます。測定には精密なノギスや内径測定器を使用し、寸法表の基準値と許容差を厳格に適用します。
施工時の品質管理では、差し込み長さの管理が最も重要です。不足すると接続強度が低下し、過剰になると継手内部で応力が集中し破損の原因となります。現場では、管端面に差し込み深さのマーキングを行い、目視で確実に管理することが効果的です。
接着剤の適用についても、寸法表の情報を活用した適切な管理が必要です。継手の肉厚や内径に応じて、最適な接着剤量と塗布範囲を決定することで、確実な接着強度を確保できます。
完成後の性能確認では、設計圧力での漏れ試験を実施します。特に大口径継手や分岐継手では、応力集中が発生しやすいため、規定圧力の1.5倍程度での長時間試験を行うことが推奨されます。
また、継手の経年劣化についても理解しておくことが重要です。紫外線や温度変化による寸法変化は微小ですが、長期間にわたって蓄積されると接続部の緩みにつながる可能性があります。定期点検では、外観変化とともに寸法変化についても確認することで、予防保全につなげることができます。
現場での実践的な品質管理として、継手種類ごとの標準作業手順書を作成し、寸法表の情報を盛り込むことが効果的です。作業者が寸法表を正確に理解し、適切に活用できる体制を整備することで、安定した施工品質を実現できます。