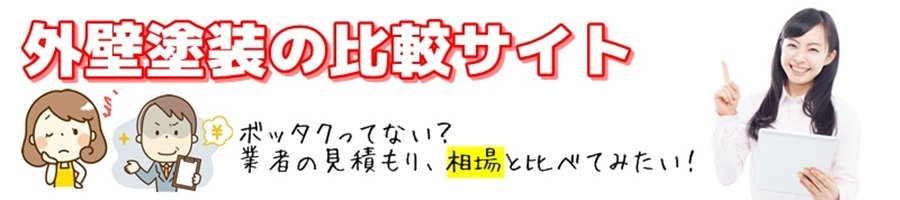
銅管の溶接が難しいとされる主な理由は、銅という素材そのものの物理的特性にあります。最も大きな課題となるのが、銅の非常に高い熱伝導率です。銅の熱伝導率は385W/m・Kで、これは鉄(63W/m・K)の約6倍、ステンレス(16W/m・K)の約24倍、アルミニウム(121W/m・K)の3倍にも達します。
この高い熱伝導性により、溶接時に発生する熱が溶接部から周囲の母材へと急速に拡散してしまいます。そのため、溶接部を適切な温度まで加熱することが困難となり、良好な溶接継手を形成するのに必要な局所的な溶融状態を維持することが難しくなるのです。
加えて、銅は酸化しやすい性質も持っています。高温になると銅の表面に酸化膜が形成され、これが溶接品質に悪影響を及ぼします。溶接部の強度低下や気孔の発生原因となるため、溶接時には不活性ガスによる適切なシールドが必要不可欠です。
また、純銅の融点は約1083℃と比較的低く、溶接時の温度管理も繊細さが求められます。熱が急速に拡散するため、十分な熱を供給しようとすると溶接部が過熱状態になりやすく、母材の変形や溶け落ちといった問題を引き起こす可能性があります。
これらの特性から、銅管の溶接には高度な技術と経験、そして適切な設備が必要とされるのです。しかし、適切な溶接方法と条件を選択することで、十分に実用的な銅管の接合が可能となります。
銅管を溶接で接合するには、その高い熱伝導率に対応できる溶接方法を選ぶことが重要です。中でもTIG溶接(タングステン不活性ガスアーク溶接)は、銅管の溶接において非常に効果的な手法といえます。
TIG溶接は、融点の高いタングステン電極と母材の間にアークを発生させ、そのアーク熱を利用して溶接を行います。この方法の最大の利点は、アークを一点に集中させることで、短時間かつ高速に局所的な加熱が可能となる点です。これにより、銅の高い熱伝導率による熱拡散の問題を最小限に抑えることができます。
TIG溶接で銅管を溶接する際のテクニックとしては、以下のポイントが挙げられます。
特に厚みのある銅管(3mm以上)を溶接する場合は、溶接部の割れを防止するために予熱が推奨されます。予熱温度は通常200〜300℃程度で、電気抵抗加熱や赤外線電気ヒーター、手動バーナーなどを用いて行います。予熱により熱拡散速度を下げ、溶接部の冷却速度を適正化することができます。
また、アークの時間を制御する専用装置(TIGCON-Tなど)を使用することで、銅管溶接の精度と再現性を高めることができます。これにより、アークを長時間当て続けることによる過熱や溶け落ちを防止し、安定した溶接品質を確保できます。
銅管の接合方法として、溶接とろう付け(ロウ付け)という二つの主要な技術があります。これらは似ているようで異なるプロセスであり、それぞれに適した用途があります。
溶接は、母材同士を溶融させて直接接合する方法です。母材と同じ成分の溶加材を使用することが多く、接合部の強度は母材とほぼ同等になります。一方、ろう付けは母材を溶かさず、母材よりも融点の低い充填金属(ろう材)を溶かして接合する方法です。毛細管現象を利用して継手の隙間にろう材を流し込み、冷却固化させて接合します。
銅管の場合、特に配管工事ではろう付けが広く採用されています。その理由は以下のとおりです。
銅管のろう付けには一般的に以下の手順が必要です。
ろう材の選択も重要で、一般的な銅配管では、銀ろうや銅リンろうが使用されます。銀ろうは約620℃〜730℃、銅リンろうは約710℃〜820℃の融点を持ち、使用環境や要求される強度に応じて選択します。
ただし、高い圧力や温度にさらされる環境、あるいは特に高い強度が求められる場合には、TIG溶接などの溶接法が選択されることもあります。用途に応じた適切な接合方法の選択が、銅管工事の成功の鍵となります。
産業現場では、銅管とステンレスやアルミニウムなどの異なる金属を接合する必要が生じることがあります。異種金属の溶接は一般的に困難とされていますが、適切な技術と方法を用いることで実現可能です。
特に注目すべき事例として、SUS304(ステンレス鋼)と銅管の接合があります。これらの異種金属は熱膨張率や熱伝導率が大きく異なるため、従来は機械的な接合や特殊なフランジを用いることが一般的でした。しかし、近年の溶接技術の進歩により、直接的な溶接接合も可能になっています。
例えば、外径12mm、厚さ1mmのSUS304パイプとC1220銅パイプの突き合わせ接合では、レーザー溶接が効果的です。レーザー溶接は熱影響が局所的で、熱変形が少ないという特徴があります。このケースでは、SUS304と、ベリリウム銅の溶接棒を使用することで、美しい外観と高い接合強度を実現しています。
TIG溶接による異種金属接合も実績があります。SUS304の板に銅パイプを溶接する場合、以下のポイントが重要となります。
異種金属溶接の課題として、ガルバニック腐食(異種金属接触腐食)のリスクがあります。これは電位差のある金属が電解質溶液(水など)と接触した際に発生する腐食現象です。この対策として、溶接部の適切な表面処理や防食コーティングの適用が重要です。
また、近年では摩擦攪拌接合(FSW)などの固相接合技術も、銅管と異種金属の接合に応用されています。これらの先進技術は従来の溶融溶接の課題を克服し、より信頼性の高い異種金属接合を可能にしています。
銅管の溶接作業を成功させるためには、適切な前処理が不可欠です。また、銅の特性に起因する特有のリスクに対応するための安全対策も重要となります。
銅管溶接の前処理として特に重要なのが、接合面の徹底的な清浄化です。銅表面の酸化膜や汚れ、油脂などは溶接品質に直接影響します。以下の前処理ステップを確実に行いましょう。
前処理が不十分だと、溶接部に気孔(ブローホール)や融合不良などの欠陥が生じやすくなります。特に銅は酸素との親和性が高いため、表面の酸化物除去は溶接品質を左右する重要なポイントです。
安全面では、銅の高い熱伝導率に起因する特有のリスクがあります。銅は熱を素早く伝えるため、溶接部から離れた場所でも高温になり、火傷の危険性が高まります。また、銅の蒸気は有害であり、適切な換気が必要です。以下の安全対策を講じましょう。
さらに、銅管溶接に特化した工具と装備の準備も重要です。
これらの前処理と安全対策を徹底することで、銅管溶接の品質向上と作業者の安全確保を両立させることができます。銅の特性を理解し、それに応じた適切な対応を行うことが、成功への近道となります。
以上、銅管の溶接に関する基本的な知識から実践的なテクニック、そして安全対策まで解説しました。銅の高い熱伝導率という特性は確かに溶接を難しくしますが、適切な知識と技術、そして準備があれば、十分に対応可能です。TIG溶接やレーザー溶接などの最新技術を活用し、銅管溶接の課題を克服していきましょう。