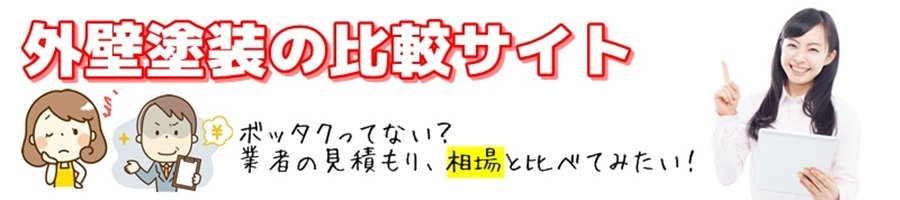
腐食性物質と金属の反応は、主に電気化学的な酸化還元反応によって進行します。この反応では、金属がアノード(陽極)として作用し、電子を失ってイオン化することで腐食が始まります。
腐食の進行パターンは環境条件によって大きく4つに分類されます。
特に酸性環境では、pH4以下になると腐食が大幅に加速されることが知られています。これは水素イオン濃度の増加により、金属からの電子放出が促進されるためです。
湿度も重要な要因で、空気中の水分が金属表面に結露することで電解質となり、腐食反応を活発化させます。海岸地帯では海塩による塩化物イオンの影響で、より激しい腐食が発生することも確認されています。
耐食性の高い金属材料の選定は、使用環境の特性を十分に理解した上で行う必要があります。金属の腐食抵抗性は、主に以下の3つのメカニズムによって発揮されます。
貴金属系材料
金やプラチナ、パラジウムなどの貴金属は、分子構造が非常に安定しており、金属イオンが溶け出しにくい特性があります。これらの材料は硫酸や硝酸、塩酸でも溶解しないため、極めて過酷な腐食環境での使用が可能です。
不動態皮膜形成材料
ステンレス鋼、アルミニウム合金、チタン合金、ニッケル合金などは、表面に極薄の不動態皮膜を形成することで耐食性を発揮します。特にSUS316は、モリブデン(Mo)2.5%の添加により、海水や塩化物環境において高い耐食性を持ちます。
保護錆形成材料
銅や亜鉛、耐候性鋼などは、表面に形成される錆自体が保護層として機能し、内部への腐食進行を防ぎます。部分的な損傷があっても自己修復機能により新たな保護層が形成されます。
高性能合金材料
表面処理技術は、金属本体を腐食性物質から保護する最も効果的な手段の一つです。適切な表面処理により、材料の寿命を大幅に延長することが可能になります。
メッキ処理
亜鉛メッキは最も一般的な防食処理で、亜鉛が鉄よりもイオン化傾向が大きいことを利用した犠牲防食効果を発揮します。メッキ層に傷がついても、亜鉛が優先的に腐食することで鉄の保護が継続されます。
アルマイト処理
アルミニウム合金に対するアノード酸化処理で、表面に厚い酸化皮膜を人工的に形成します。この皮膜は非常に硬く、耐摩耗性と耐食性を同時に向上させることができます。
最新のアノード酸化技術
近年の研究では、硝酸系水溶液を用いたチタンのアノード酸化により、多孔質TiO2-TiN系複合酸化皮膜の創製が可能になっています。この技術により、従来のフッ化物系電解液の課題であったコストと環境負荷の問題を解決できる可能性があります。
特殊コーティング技術
表面処理の選択にあたっては、基材の種類、使用環境の厳しさ、要求される寿命、コスト等を総合的に評価することが重要です。
腐食性物質に対する材料の適合性を正確に評価するためには、体系的な試験方法と評価基準が必要です。材料評価は実際の使用環境を模擬した条件下で実施することが重要です。
腐食速度の定量評価
腐食の強さを表す指標として、「侵食度」が用いられます。一般的には以下の単位で表現されます。
腐食形態の分類と評価
腐食は大きく「全面腐食」と「局部腐食」に分けられます。局部腐食には以下のような種類があります。
環境条件の影響評価
腐食促進因子の定量的評価も重要です。
試験方法の標準化
JIS(日本産業規格)やASTM(米国材料試験協会)などの規格に基づいた標準試験により、材料間の客観的比較が可能になります。試験期間や条件の設定により、長期使用における信頼性を予測できます。
従来の事後対応型メンテナンスから予防的保全への転換は、設備の長寿命化とコスト削減を実現する重要な戦略です。IoT技術とデータ分析を活用した新しいアプローチが注目されています。
スマートモニタリングシステム
センサー技術の進歩により、腐食の初期段階での検出が可能になっています。以下のような監視手法が実用化されています。
環境制御による根本対策
腐食環境そのものを改善することで、材料への負荷を軽減します。
メンテナンス計画の最適化
データに基づいた科学的なメンテナンス計画により、効率的な設備管理が実現できます。
人材育成と技術継承
腐食対策の成功には、現場作業者の知識とスキル向上が不可欠です。定期的な教育プログラムと実践的な訓練により、予防保全の効果を最大化できます。
金属加工現場における腐食性物質への対応は、材料選定から表面処理、環境管理、モニタリングまでの総合的なアプローチが重要です。最新技術を活用しながら、現場の実情に合わせた対策を継続的に改善していくことで、設備の信頼性向上とコスト削減を同時に実現できます。
厚生労働省の化学物質管理ガイドライン
https://www.mhlw.go.jp/content/11303000/000592181.pdf