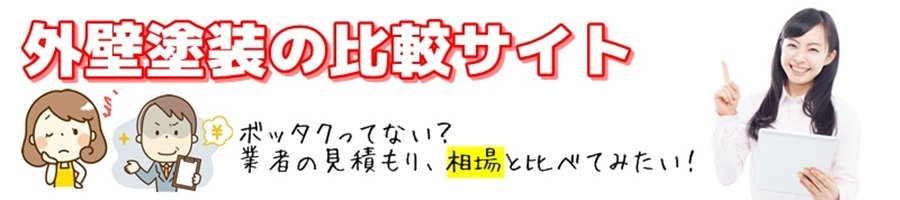
電線管サイズ表を効果的に活用するには、まず各種規格の特徴を理解することが重要です。金属加工現場で使用される電線管は主に4つのカテゴリーに分類されます。
厚鋼電線管の規格特性
厚鋼電線管は最も堅牢性に優れた電線管で、G16からG104まで10種類の規格があります。特に注目すべきは、管の呼び方と実際の内径の関係です。
興味深いことに、厚鋼電線管の厚さは2.3mmから3.5mmまで段階的に変化しており、大径になるほど厚肉構造となっています。これは構造強度と経済性のバランスを考慮した設計思想の表れです。
薄鋼電線管との使い分け
薄鋼電線管(C19、C25等)は厚鋼電線管と比較して、同等の内径でも外径が小さく設計されています。例えばC19は外径19.1mm、内径15.9mmで、厚さはわずか1.6mmです。金属加工現場では、スペース制約がある場所や軽量化が求められる用途で重宝されています。
塩ビ管規格の特殊性
塩ビ管は数字のみで呼び方が表記され、14から82まで9種類の標準規格があります。塩ビ管14は外径18mm、内径14.0mmで、断面積は153mm²となっています。金属加工における腐食性環境や屋外配管では、塩ビ管の耐候性が大きな優位性を発揮します。
電線管サイズ表を使った選定では、電線の断面積と本数から必要な管内断面積を算出することが基本となります。この計算プロセスを正確に理解することで、過剰設計や容量不足を防げます。
断面積計算の基本公式
電線管内の電線収容率は、安全性と施工性を考慮して40%以下に制限されています。つまり、必要な電線総断面積を0.4で除した値が、最小限必要な管内断面積となります。
計算式:必要管内断面積 = 電線総断面積 ÷ 0.4
例えば、直径2.0mmの電線(断面積3.14mm²)を10本収容する場合。
電線総断面積 = 3.14 × 10 = 31.4mm²
必要管内断面積 = 31.4 ÷ 0.4 = 78.5mm²
この場合、断面積153mm²の塩ビ管14または断面積211mm²の厚鋼電線管G16が適用可能です。
安全率を考慮した選定方法
実際の現場では、将来の配線追加や施工時の余裕を考慮して、計算値より1サイズ大きい電線管を選定することが一般的です。これは「余裕率20%」と呼ばれる実務慣行で、長期的な設備運用を考慮した賢明な判断といえます。
特殊条件での補正計算
金属加工現場特有の条件として、高温環境や振動環境では電線の劣化が早まる可能性があります。このような場合は標準収容率を35%程度に下げて計算することが推奨されます。
また、曲がり部分が多い配管では、電線の引き抜き抵抗が増加するため、直線部分より大きなサイズの電線管を選定する必要があります。曲がり半径は電線管内径の6倍以上を確保することが施工上の基本ルールです。
電線管サイズ表を配管工事で効率的に活用するには、現場特性に応じた実践的なテクニックが必要です。金属加工業界での配管工事は、他業界と比較して特殊な要求事項が多く存在します。
プリカチューブの戦略的活用
可とう性が要求される箇所では、プリカチューブが威力を発揮します。プリカチューブの規格表を見ると、呼び方10から63まで9種類があり、最小内径と外径の関係が通常の電線管と異なります。
金属加工機械の可動部分や振動が激しい箇所では、プリカチューブの柔軟性が配線の断線リスクを大幅に軽減します。
曲げ加工時の径選定ノウハウ
電線管の曲げ加工では、ハイベンダーE型などの専用工具を使用しますが、曲げ半径は管内径の約6倍が基本です。この制約により、狭い場所での配管では必然的に小径の電線管を選択せざるを得ない場合があります。
実務上のコツとして、90度曲げが必要な箇所では、直線部分より1サイズ大きい電線管を使用し、曲げ部分で内径が減少する影響を補償する方法があります。
リングレジューサーの効果的利用
異なるサイズの電線管を接続する際は、リングレジューサーを活用します。例えば、G22用のリングレジューサー(品番DF0022P)は、ノックアウト径が電線管より大きい場合の接続に使用され、配管システム全体の柔軟性を向上させます。
配管ルート設計の最適化
金属加工現場では、工作機械の配置変更が頻繁に発生するため、将来の変更に対応できる配管設計が重要です。主要ルートには大径の電線管を使用し、分岐部分で適切なサイズに分割する「幹線・分岐方式」が効果的です。
電線管サイズ表を使用した選定でも、実際の施工段階で予期しないトラブルが発生することがあります。これらのトラブルパターンを事前に把握し、対策を準備することが重要です。
電線収容限界の誤算対策
最も頻繁に発生するトラブルは、電線収容率の計算ミスです。特に異なる太さの電線を混在させる場合、単純な断面積計算では不十分な場合があります。
実際の対処法として、混合配線では最大径電線の断面積を1.2倍で計算し、小径電線との隙間を考慮することが推奨されます。また、制御線と電力線を同一管内に収容する場合は、ノイズ対策として追加のシールド線を想定し、収容率を30%程度に下げた計算が安全です。
熱膨張による配管破損防止
金属加工現場では、溶接作業や熱処理工程により周辺温度が上昇します。電線管も熱膨張するため、長尺配管では伸縮継手の設置が必要です。
厚鋼電線管の線膨張係数は約12×10⁻⁶/℃で、10mの配管が50℃上昇すると6mm伸縮します。この変化を吸収するには、50m間隔で伸縮継手を設置することが目安となります。
電食腐食の予防策
異なる金属の電線管を接続する際は、電食腐食に注意が必要です。例えば、アルミ製プリカチューブと鋼製電線管を直接接続すると、接触部分で腐食が進行します。
この問題は、樹脂製の絶縁リングを挟むことで解決できます。また、屋外や湿気の多い環境では、定期的な防食処理が腐食進行を遅らせる効果的な対策となります。
施工後の点検チェックポイント
配管完了後は、以下の項目を重点的にチェックします。
これらの点検を怠ると、運用開始後に配線トラブルが発生し、生産停止につながるリスクがあります。
電線管サイズ表を活用した設備は、適切なメンテナンス管理により長期間の安定運用が可能になります。金属加工現場特有の過酷な環境条件を考慮した、実践的な管理手法を解説します。
定期点検スケジュールの策定
電線管システムの点検頻度は、設置環境と管種により異なります。一般的な点検サイクルは以下の通りです。
金属加工現場では、切削油や金属粉塵の付着により腐食が加速するため、標準より短いサイクルでの点検が推奨されます。
劣化診断の技術的手法
電線管の劣化状態は、目視だけでは判断が困難な場合があります。以下の診断手法を組み合わせることで、正確な状態把握が可能です。
肉厚測定による残存寿命予測
超音波厚さ計を使用し、電線管の肉厚を測定します。厚鋼電線管G22(標準厚さ2.3mm)の場合、1.8mm以下になると交換時期の目安となります。
絶縁抵抗測定によるトラブル予兆発見
配管内の電線について、定期的な絶縁抵抗測定を実施します。測定値が前回比で30%以上低下した場合は、管内への水分浸入や電線被覆の劣化が疑われます。
予防保全のコスト効果分析
適切なメンテナンス投資により、設備の総ライフサイクルコストを大幅に削減できます。実際の事例では、予防保全により以下の効果が確認されています。
これらの効果は、電線管サイズ表を適切に活用した初期設計と、継続的なメンテナンス実施の相乗効果によるものです。
デジタル管理システムの導入
最新の設備管理では、QRコードやRFIDタグを電線管に貼付し、点検履歴をデジタル化する手法が普及しています。この方法により、点検漏れの防止と効率的な作業管理が実現できます。
また、IoTセンサーを主要な電線管に設置し、温度や振動データをリアルタイムで監視することで、予兆保全の精度向上が期待できます。
金属加工現場における電線管サイズ表の活用は、単なる選定作業にとどまらず、設備全体の信頼性向上と生産性向上に直結する重要な技術要素です。適切な規格選択、計算に基づく設計、実践的な施工テクニック、そして継続的なメンテナンス管理を総合的に実践することで、長期間にわたる安定した電気設備運用が実現できます。
電材ネットによる最新の電線管規格情報
https://www.denzai-net.jp/technical/den_technical_dk-01.htm
宮地電機による詳細な電線管規格表
https://www.miyajidenki.com/office-environment-i/technical_01/