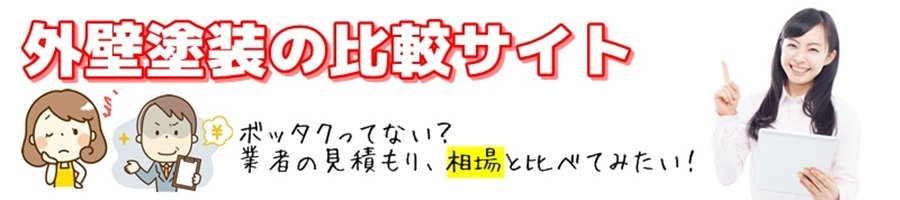
リップみぞ形鋼は、JIS G 3350:2021「一般構造用軽量形鋼」として規格化された重要な建築用鋼材です。この規格では、リップ溝形鋼の正式な定義として、軽溝形鋼にリップ(唇状の補強部)を付加した断面形状を持つ薄肉鋼材として位置づけられています。
JIS規格の基本要件:
リップ部の存在により、同一寸法の軽溝形鋼と比較して断面二次モーメントが15-20%向上し、構造性能が大幅に改善されています。この補強効果により、より細い断面で同等の強度を確保できるため、建築物の軽量化に大きく貢献しています。
形鋼の分類において、リップ溝形鋼は「一般構造用軽量形鋼」の中でも特に汎用性が高く、H形鋼、山形鋼、ハット形鋼と並んで重要な位置を占めています。その形状的特徴から「Cチャンネル」「Cチャン」とも呼ばれ、現場では両方の呼称が混在して使用されています。
JIS規格に基づくリップ溝形鋼の標準寸法は、用途に応じて幅広いサイズ展開が規定されています。以下に代表的な規格寸法と断面性能を示します。
小型サイズ(軽量用途):
規格記号 | 高さ(mm) | 幅(mm) | リップ(mm) | 厚さ(mm) | 単位質量(kg/m) |
---|---|---|---|---|---|
C-40×20×10 | 40 | 20 | 10 | 1.6 | 1.14 |
C-60×30×10 | 60 | 30 | 10 | 1.6-2.3 | 1.65-2.28 |
C-75×45×15 | 75 | 45 | 15 | 1.6-2.3 | 2.35-3.28 |
中型サイズ(一般構造用):
規格記号 | 高さ(mm) | 幅(mm) | リップ(mm) | 厚さ(mm) | 単位質量(kg/m) |
---|---|---|---|---|---|
C-100×50×20 | 100 | 50 | 20 | 1.6-3.2 | 2.92-5.54 |
C-150×50×20 | 150 | 50 | 20 | 1.6-3.2 | 3.56-6.81 |
C-150×75×25 | 150 | 75 | 25 | 2.3-3.2 | 6.11-8.32 |
大型サイズ(重荷重対応):
規格記号 | 高さ(mm) | 幅(mm) | リップ(mm) | 厚さ(mm) | 単位質量(kg/m) |
---|---|---|---|---|---|
C-200×75×25 | 200 | 75 | 25 | 1.6-3.2 | 4.96-9.59 |
C-250×75×25 | 250 | 75 | 25 | 1.6-3.2 | 5.60-10.9 |
C-300×75×25 | 300 | 75 | 25 | 1.6-3.2 | 6.24-12.1 |
断面性能では、断面二次モーメント(慣性モーメント)が設計上最も重要な指標となります。例えば、C-150×75×25×2.3規格では、X軸回りの断面二次モーメントが273cm⁴、断面係数が36.4cm³となり、同等の軽溝形鋼より約18%高い性能を示します。
リップ部の寸法は、一般的に幅の1/3程度に設定されており、この比率により最適な補強効果が得られることが実証されています。また、せん断中心の位置も考慮されており、偏心荷重に対する抵抗性能も規格内で明確に定義されています。
リップ溝形鋼の材質は、JIS G 3350規格において化学成分と機械的性質が厳格に規定されています。基本的には一般構造用炭素鋼をベースとし、溶接性と加工性を重視した成分調整が施されています。
化学成分規定(質量%):
この成分調整により、優れた冷間加工性と適度な強度を両立しています。特に炭素含有量を抑制することで、ロール成形での割れ発生を防止し、安定した製造品質を確保しています。
機械的性質:
強度特性では、薄肉材特有の局部座屈現象への対策が重要となります。リップ部の存在により、フランジ部の座屈耐力が向上し、より高い許容応力での使用が可能になっています。
表面処理においては、耐食性向上のため各種めっき処理が適用可能です。一般的な亜鉛めっき(Z120、Z275)のほか、高耐食性を要求される用途では、アルミニウム・亜鉛合金めっきや有機系被膜処理も選択できます。
溶接性については、薄肉構造のため通常の溶接は困難ですが、適切な条件下でのスポット溶接や低入熱溶接は可能です。ただし、実際の施工では機械的接合(ボルト、リベット、セルフタッピングスクリュー)が主流となっています。
リップ溝形鋼の加工において最も重要な特徴は、薄肉構造による優れた切断・穴開け加工性と、一方で溶接加工の制約です。実際の製造現場では、この特性を活かした効率的な加工方法が確立されています。
切断加工の実務:
切断時の注意点として、リップ部の変形防止が重要です。特に薄肉材では、クランプ圧が過大になると局部的な座屈が発生するため、適切な支持方法の選択が必要です。
穴開け加工の技術:
穴開け加工では、ドリル加工、ポンチング、レーザー加工が主流です。リップ部近傍への穴開けでは、リップの補強効果を損なわないよう、端距離を板厚の3倍以上確保することが実務上の基準となっています。
曲げ加工における課題と対策:
リップ溝形鋼の曲げ加工は、リップ部の存在により複雑な応力分布が生じます。プレスブレーキでの加工では、以下の点に注意が必要です。
接合方法の選択指針:
溶接接合は薄肉のため熱影響による変形リスクが高く、実務では機械的接合が圧倒的に多用されています。
接合部の設計では、リップ溝形鋼の断面が左右非対称であることから、偏心モーメントの発生を考慮した配置が重要です。特に2本の背中合わせ接合では、偏心の影響を相殺でき、より高い耐力を発揮できます。
リップ溝形鋼の規格選定において、単純な強度計算だけでは不十分な場合があります。薄肉構造特有の座屈現象や、使用環境に応じた表面処理の選択など、実務的な配慮が設計品質を大きく左右します。
座屈現象への対策:
薄肉材では、全体座屈より局部座屈が先行して発生することが多く、従来の強度計算では安全性を正しく評価できません。特に以下の座屈モードに注意が必要です。
実務では、これらの座屈耐力を個別に検討し、最小値が許容応力となります。最新のJIS G 3350:2021では、これらの座屈現象を考慮した設計法が明確化されています。
環境条件に応じた仕様選定:
使用環境により、表面処理の選択が重要な決定要因となります。
品質管理の実務ポイント:
リップ溝形鋼の品質管理では、以下の項目が特に重要です。
製造メーカーの選定では、JIS認証取得の有無だけでなく、品質管理体制の実態確認が重要です。特に寸法精度については、統計的品質管理(SQC)を導入しているメーカーを選択することで、施工時のトラブルを大幅に削減できます。
設計における留意事項:
実際の設計では、理論値と実際の性能に差が生じる場合があります。特に以下の点は実務経験に基づく配慮が必要です。
これらの要因を総合的に判断し、適切な安全率を設定することが、信頼性の高い設計につながります。最新の設計基準では、これらの実務的な課題も反映されており、規格の継続的な改訂により実用性が向上しています。